-
11.6分 | 4613阅读 | 4人下载
-
20.9分 | 2905阅读 | 3人下载
-
31.9分 | 13158阅读 | 6人下载
-
42.2分 | 13064阅读 | 3人下载
-
52.5分 | 10161阅读 | 14人下载
-
61.5分 | 7592阅读 | 8人下载
-
71.5分 | 6835阅读 | 5人下载
-
81.1分 | 6079阅读 | 4人下载
-
91.3分 | 6059阅读 | 8人下载
-
102.7分 | 5756阅读 | 1人下载
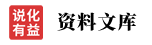




有色金属铝合金工件的表面处理工艺
铝合金制品的表面处理
第一章 概 述
一、 铝及铝合金表面处理的目的:(主要指阳极氧化)
1、 防腐蚀
天然氧化膜→薄 ,
阳极氧化膜 → 厚≥10μm
漆膜→ 耐磨、耐蚀、耐光、耐候
2、 防护 — 装饰
形成微孔人工氧化膜后,可染成各种颜色和图案。
3、 功能作用
绝缘性≥100μm
微孔渗渍硫化钼润滑剂 → 摩擦系数↓
电沉积磁性金属 → 磁性录音盘、记忆元件等等。
二、 铝及其合金表面处理的分类
机械法、化学法、电化学法、阳极化膜后处理(见后面附录)
三、 铝型材表面处理产品种类
目前市场上常见的有:
1)阳极氧化(银白、砂白料)
2)阳极氧化 + 电解着色(浅古铜、古铜、黑色等)
3)电泳涂漆
4)静电喷漆、氟碳喷漆
5)静电粉末喷涂
四、铝及铝合金表面处理工艺流程
1、建筑铝型材阳极氧化处理和喷涂工艺流程:
电泳→固化成膜
脱脂→碱蚀→中和出光→阳极氧化(DC法)→电解着色(AC法)→封孔
脱脂→酸洗→化学转化→静电喷涂 →固化成膜
2、通用工业用铝合金部件(机械部件、电器部件等)阳极氧化处理工艺流程:
草酸法
脱脂→酸洗→中和出光→阳极氧化→硫酸法(染色)→封孔
硬质阳极氧化法
3、装饰用铝合金部件(汽车装饰部件、照相机部件等)阳极氧化处理工艺流程:
机械喷砂 染色→印刷
(人工修整→振动抛光)→脱脂→化学炮光 →阳极氧化(硫酸法)→封孔
电化学抛光
第二章 铝材阳极氧化前的处理
铝合金建筑型材生产工艺流程:
铝材装架 → 脱脂 → 水洗 → 碱蚀 → 水洗(二道)
→ 中和(出光)→ 水洗 → 阳极氧化(DC法)→ 水洗→ 封孔
水洗→着色(AC法)→水洗
→水洗→ 卸架
第一节 装 架
一、 方式:横吊式、竖吊式
纵吊式特点:
1、 适合大批量生产:每批可装载大量铝材
2、 减少装卸工人:减轻了装卸时的劳动力
3、 降低生产成本:溶液带出量少,减少化学品消耗量,夹具不浸入处理液中,减少夹具消耗量。
4、 减少用水量:带出水量减少,耗水量及废水处理量减少。
适于生产能力在600吨/月以上。
目前,一般采用横吊式为多。
二、 注意事项:(横吊式)
1)铝材要有一定倾角(3º~ 5º)→ 便于氧化时气泡逸出。
2)扎料要紧,导电杆脱模要干净 →保证导电良好。
3)每根料之间间距应保证→ 防止色差。
4)避免不同型号、长度的料扎在一起着色→ 防止色差。
5)每次上料面积要一定,最好是对极面积的80%,最大100%。
第二节 脱脂处理
一、 目的:
除去制品表面的工艺润滑油、防锈油及其他污物,以保证在碱
洗工序中,制品表面腐蚀均匀和碱洗槽的清洁,从面提高氧化制品质量。
二、 油脂种类:
动物油、植物油→属皂化油,可与苛性碱发生皂化反应
矿物油→属非皂化油,不与苛性碱发生皂化反应
锯切液
三、 脱脂方法与原理
1) 有机溶剂:酒精、煤油、汽油、丙酮、甲苯、三氯乙烯、四氯化碳等。利用溶剂对油污很强的溶解能力将油除去。对Al基体无腐蚀性。
2) 表面活性剂:合成洗涤剂、金属清洗剂等。利用有效成份对油污的优良的皂化、乳化、分散、渗透能力将油污除去,对铝基体无腐蚀作用。
3) 碱性溶液:NaoH + 添加剂(乳化剂)
利用溶液中的某些碱性物质与油污发生皂化或乳化作用来达到除油污之目的。
皂化作用—→除去动、植物油
乳化作用—→除去矿物油
皂化反应:
CH(CHCOO)+3NaOH→ 3CHCOONa+3CH(OH)
硬脂酸 苛性钠 肥皂 甘油
乳化作用:略
成份及其作用:
1 NaOH:皂化反应,除油作用。
2 NaCO(碳酸钠)、NaPO(磷酸三钠):缓冲剂,保持溶液PH=10~11。
3 硅酸钠(水玻璃):湿润剂、乳化剂、分散剂,不易水洗去掉
4) 酸性溶液
HSO、HNO等
Al + HSO= Al(SO)+ H↑
利用H小泡包围油珠,离开铝表面层达到除油目的。
5) 电解脱脂
即将制品放在碱性溶液中作为阴极而进行电解处理除去油污。
四、 脱脂工艺制度
轻油级:
1)HSO150 ~ 250g/l 常温3 ~ 5分钟
2)HNO150 ~ 200g/l 常温2 ~ 3分钟
3)HNO120 ~ 150g/l
HSO120 ~80g/l 常温2 ~ 5分钟
重油级:
1)NaPO40 ~ 60g/l (弱碱性)
NaOH 8 ~ 12g/l
NaSiO20 ~ 30g/l 50 ~ 60℃ 2 ~ 3分钟
2)NaPO30g/l
NaCO20g/l 40℃ 2 ~ 3分钟
3)金属清洗剂
20 ~ 30g/l 常温 5 ~ 8分钟(根据说明书要求)
碱性除油工艺:
NaOH 10 ~ 15g/l ,添加剂 20 ~ 30g/l,45 ~ 60℃,3 ~ 7分钟
第三节 碱 蚀
一、 目的:
1) 除去铝材表面的自然氧化膜,使金属基体暴露出来,
活化表面,有利于氧化着色。
2) 整平基体表面,使其均匀一致。
3) 调整金属光泽。
4) 进一步除去铝材表面污物。
二、 方法:
碱法、磷酸钠法、硫酸铬酸法等。
一般采用强碱热溶液。
三、 碱蚀原理:
碱蚀过程主要有以下三步化学反应:
AlO+ 2NaOH → 2NaAlO+ HO
2Al + 2NaOH + 2HO → 2NaAlO+ 3H↑
2NaAlO+ 4HO → 2Al(OH)↓+ 2NaOH
AlO↓+3HO
第一步反应是除去铝材表面的天然氧化膜;
第二步是铝基体与碱反应,起整平表面的作用;
第三步是前二步反应所生成的偏铝酸钠不断水解,生成胶状的氢氧化铝和苛性钠,氢氧化铝进而脱水变成AlO硬水铝石。
现在工业上普遍使用长寿命碱蚀添加剂。
四、 添加剂的作用:
具有防止产生铝石、增光、整平、缓蚀等多种作用。
特点:
1) 允许溶存Al铝量达100g/l(甚至120g/l)以上,而不会产生硬水铝石,即使偶有发生水解也不结块,易于清除。
2) 具有缓蚀整平功能,碱蚀效果更好。
3) 铝腐蚀率能保持在1 ~ 2%之间,减少铝溶蚀量及氢氧化钠消耗量。
成份:
一般有葡萄糖酸钠、酒石酸盐、柠檬酸盐、羧甲基纤维素等多元多组份的混合物。
五、 碱蚀工艺:
NaOH:50 ~ 60 g/l,碱蚀添加剂:视说明书要求,温度:50 ~ 70℃
时间:视工艺要求
第四节 中 和(出光)
一、 目的:①中和残碱,防止污染氧化槽。②洗去残留在表面的Cu、Fe、Zn、Si、Mn等元素的氧化物(挂灰),光亮表面。
二、 方法:
1) 硝酸法:HNO150 ~ 250g/l,温度室温,时间:1 ~ 3分钟
为氧化性酸,出光效果较好,但成本高,易污染氧化槽,烟雾大。
2) 硫酸法 :HSO150 ~ 250g/l,温度:室温,时间:3 ~ 5
分钟。出光效果不甚理想,可加入少量氧化剂(HNO、HO),以增强其氧化性,或加入添加剂。不污染氧化槽,成本低。
3) 硝酸 + 氢氟酸(3 :1体积比)
用于高硅铝合金、铸造铝合金。
第五节 特殊要求预处理
一、消光处理
1、化学方法:
1)NaOH溶液(全面均匀腐蚀)
浓度:5~25%,温度:50~70℃,时间:1~10min
2)NHHF +(NH)SO溶液(斑点腐蚀)
3)NHF溶液(斑点腐蚀)
浓度:3~5%,温度:20~40℃,时间:1~5min
2、电化学方法(电解消光处理法):
1)HCl溶液
浓度:5 ~ 20%,温度:20~60℃,时间:1~2min,
电流密度:10~30A/dm
2)HCl + HSO溶液
HCl浓度:0.3%,HSO浓度:1~2%,温度:75~80℃,时间:0.5~
1min,电流密度:70A/dm
3)HCl + NHCl溶液
3、机械方法:喷砂处理等等
二、抛光处理
1、化学抛光
最常用的是三酸抛光:HPO—75v/v%(体积比)、HSO—15%、HNO—10%、Cu(NO)或 CuSO少量。
抛光质量好,操作简单。缺点是成本高,污染重。代替方法是碱性抛光技术。
2、电解抛光
HPO:40~80%、HSO:4~15%、HCrO:0.2~9%、HO余
温度:70~90℃,时间:1~3min,电流密度:10~15A/dm
多用于表面光洁性要求很高的装饰材料。
3、机械抛光
设备有扫纹机、布轮等
第三章 阳极氧化
一、 目的:人为在制品表面生成(或加厚)氧化膜。
二、 方法:化学氧化、阳极氧化
第一节 化学氧化
化学氧化是在一定的温度下,使清洁的铝表面与氧化溶液中的氧发生反应而生成氧化膜的方法。
化学氧化膜与自然氧化膜相比,厚度要大100一200倍。与阳极氧化膜相比,具有以下特点:
(1)膜的生成速度快;
(2)处理设备简单,生产成本低;
(3)涂料附着性良好,耐蚀性优良;
(4)膜薄(0.5~3μm)而软,耐磨性和着色性较差。
因此,—般只用作防蚀涂漆膜的底层。在工业上,化学氧化常用于形状复杂的零件、室内装饰品以及屋面材料的氧化处理。
一、化学氧化原理
在一定温度下,在含有氧化剂(常用铬酸盐)和活化剂(常用碳酸盐)的溶液中,通过化学作用使铝离子和氧化溶液中的氧相互作用在制品表面生成一层致密氧化膜的方法。
溶液一方面应具有氧化能力,能使铝表面产生氧化膜,另一方面也应具有使氧化膜部分溶解而产生针孔的作用,促进氧化膜成长和厚度增加。但要使氧化膜在溶液中的生长速度必须大于溶解速度。
一般所采用的酸有HF、NaSiF十酸、铬酸、酒石酸、磷酸等;采用的碱性盐为铬酸盐、磷酸盐等。
化学氧化所采用的溶液的种类是很多的,最常用的是含有碳酸钠作为活化剂的溶液中进行化学氧化处理。
二、化学氧化处理法
现代一般广泛使用的铝及铝合金的化学氧化膜的处理方法有:饱尔—福格耳法(BV法)、MBV法、E.W法、派卢明法、阿尔罗克法、阿洛克罗姆法等。
按溶液的组成可分为:
(1)以碳酸钠为主体;
(2)以铬酪或重铬酸盐为主体;
(3)以氟化物为主体;
(4)以磷酸为主体。
作为铝合金建筑型材粉末喷涂前的预处理,常用的化学氧化膜有铬酸膜、磷酸膜和新开发的无铬膜。
第二节 阳极氧化
所谓阳极氧化——即把铝型材人为阳极置于电解液中,利用电解作用在制品表面形成多孔性的氧化薄膜。
一、阳极氧化的种类
按电流形式分有:直流电阳极氧化、交流电阳极氧化、脉冲电流阳极氧化。
按电解液分:硫酸、草酸、磷酸、铬酸、混合酸及以磺基有机酸为主的自然着色阳极氧化。
按膜层性质分:普通膜、硬质膜、瓷质膜、光干涉膜
二、阳极氧化原理
铝氧极氧化的原理实际上就是水电解的原理。
阳极: Al-3e → Al
6OH→3HO + 3O
2Al+3O→ AlO+热量(399卡)
阴极: 2H+2e → H↑
氧化膜的生成规律,可通过氧化过程的电压一时间曲线来详细说明。
条件: 20%HSO水溶液,阳极电流密度 D=1A/dm,
温度 22℃.
第一段(曲线ab段):
在通电十几秒内电压急剧上升,这是由于铝表面形成了连续的、无孔的氧化膜,叫做活性层。由于它具有半导体整流作用,所以又叫阻挡层。
第二段(曲线bc段):
当电压达到一定数值后,开始下降,一般比最高值下降10 ~ 15%,
这是由于电解液对氧化膜的溶解作用所致,使铝表面产生无数微观孔穴,从而保证电流能够顺利通过。
第三段(曲线cd):
阳极氧化经过20秒以后,电压下降至一定数值就趋于稳定,然后以缓慢的速度上升。这时无孔层的生成速度和溶解速度达到平衡,其厚度不再增加。但氧化反应并未停止,在每个孔穴底部,活性层通过溶解、再生,随时间延长而向纵深发展最后形成了六梭体蜂窝状氧化膜结构,即多孔质层。
活性层厚度约为15×10m,针孔内径为10~15×10m,壁厚12~15×10m,针孔密度大约为4~5亿个/m,硫酸阳极氧化膜的孔隙率为20 ~ 30%。
三、氧化膜厚度
δ—氧化膜厚度,μm
I—电流密度,A/dm
t—氧化时间,min
K为常数,与电流效率和某一工艺条件下生成膜的密度或孔隙度有关。我国采取K = 0.25~0.26
例:某厂,20% HSO溶液,18~20℃,DC法
D=1.4A/dm, t=30min , δ=12~13μm.
由δ=K·I·t →K=≈0.286
四、直流硫酸阳极氧化工艺规范
电 流——直流电DC
电解液——硫 酸
铝及铝合金阳极氧化膜的优点:
1、可大大提高铝材表面的耐磨、耐蚀、耐光、耐候及着色性能。
2、由于氧化膜是由基体金属直接生成的,所以与基体结合牢固,很难用机械的方法从基体金属上分离去掉。
3、氧化膜有良好的绝缘性。
直流电硫酸阳极氧化工艺:
参数名称 | 通常使用范围 | 最佳条件 |
HSO含量 | 150~200g/l | 180g/l |
Al离子含量 | <20g/l | 5g/l |
温度 | 18~22℃ | 20℃ |
电流密度 | 1~2A/dm | 1.2~1.5A/dm |
时间 | 按膜厚要求而定 | 30 分钟 10μm 60分钟 18μm |
电压 | 16 ~ 21V | 17 ~ 19V |
极比 | 阴极∶工件=1∶2.5 | 1∶1 |
五、影响阳极氧化膜质量的因素:
1、 硫酸浓度
浓度↓ 膜亮度↓从无色透明→灰色;溶液电阻↑→槽电压↑浪费电能。
浓度↑成膜速度↓(膜溶解速度↑);膜质量软;电解质粘度↑→水洗困难。
工业实际使用范围150~200g/l.
2、 电流密度
由δ=K·I·t可知:膜厚δ由I及t决定,I↑、t↓→生产率↑。
I大小对膜质量有影响:I↓膜结构致密、硬;I↑膜易“烧焦”,膜厚不均匀性↑(大面料、复杂料)。一般采用1.2~1.5A/dm。
3、 槽液温度
槽液温度↓(如0~5℃)氧化膜发脆, 膜层透明度与染色性能↓(即吸附性能)。
槽液温度↑(如≥25℃)氧化膜疏松,(呈蜂窝状晶体,壁厚减薄),甚至起白粉。理想的温度为20±2℃。
恒温方式:加热——蒸汽,冷却——冷冻机或加添加剂。
4、 电解电压
由于采用定电压阳极氧化则很难控制膜厚,铝合金硫酸阳极氧化采用定电流工作方式。电解电压根据设定电流密度来确定,一般在10~22伏范围内,最佳范围15~17V。
5、 氧化时间
在恒电流的条件下,由δ= K·I·t可知成膜时间和膜厚成正比。
6、 杂质的影响
(1)合金成份:Mg > 2% 膜变暗浊色。Si > 0.8% 膜光泽↓>2%呈灰黑色,出现斑点。Cu%↑膜色调深暗或灰黑色。Zn↑膜呈灰暗色。Mn即便<0.1% 膜也带色与无光。
(2)槽液杂质: Cl、F(氟冷却液)→出现孔蚀现象。Fe→暗花纹和黑色斑点。Cu→正弦曲线状暗条纹。最好使用纯水配电解液
(3)Al离子:Al↓↓(≤0.1g/l时), 电解液溶解能力过强,膜厚↓生成困难,耐蚀、耐磨、染色等性能↓∴配槽时, 添加硫酸铝或部分老溶液。Al↑电解液电阻↑,槽电压↑,易产生白斑点,膜的耐磨、耐蚀性↓,透明性↓∴要求 Al< 20g/l。
7、搅拌(循环)
为了降温,采用槽内排管进行热交换、槽外热交换器进行热交换、压缩空气搅拌。
膜层“烧焦”、“起粉”。
影响因素:
电流密度——电流密度过高,将引起电解液温升加快,膜层溶解速度增加,对复杂工件还会造成电流分布不均,使膜层厚度不均,甚至有烧毁工件的危险。
电解液温度——温度升高,溶液粘度降低,电流密度升高(电解电压一定时)或电解电压降低(电流密度一定时)。这有利于氧化膜溶解的加剧。若同时电流密度也低,则出现粉状膜层(即起粉)。
常规的硫酸法,在低温和高电流密度时,膜层易被“烧焦”,而在高温和低电流密度时,膜层易“起粉”。
原因分析:
一般而言,阻挡层中氧化物/铝基体金属界面上总是粗糙的,即铝金属一侧存在许多凸出部位,电流往往就集中在这些部位上,造成这些部位孔的底部电流密度大,因而孔底温度受焦耳热大的影响又升高,这样又引起电流密度加大,如此恶性循环,造成氧化膜仅在工件局部位置上增厚,出现膜层“烧焦”现象,低温高电流密度时更为突出。
而“起粉”现象则是由于膜层过度化学溶解所致。
第三节 高速阳极氧化
方法:① 脉冲阳极氧化 ② 加添加剂 ③ 混合法
一、 脉冲阳极氧化
该技术电压为矩形波,有两个工作电压,即高电压V和低电压V。当用V电压进行阳极氧化时,稳定电流I通过铝阳极,阳极氧化膜形成。当电压突然从V降至V后,则出现短时内无电流通过而随之电流又逐渐增大的现象,经T分钟后才出现对应于电压V的稳定电流I通过铝阳极。电流随时间发生了畸变,这种现象叫“阳极氧化的电流恢复现象”(或称电流的回复现象),T称为电流恢复时间。
采用脉冲电流后,利用短时间的高电流密度使膜层迅速成长,在“烧焦”现象出现前,骤然将电压降至V,在电流恢复时间内,膜层成长中止,这样降低了氧化物/铝基体金属界面上的粗糙度。同时膜孔内积聚的焦耳热也得到散失,使制品各部件上温差缩小。因此,采用脉冲电流后,能较好避免“烧焦”现象的出现。由于膜孔内热量能及时得到散失,高电流密度氧化又是短时间的所以避免了膜层的过度化学溶解,于是又克服了膜层的“起粉”现象。
由此可见,脉冲电流具有许多优点:膜层性能提高,温度电流密度等操作条件范围扩大,电流效率高等。
工艺条件:
18% HSO, I = 2~3.5 A/dm, V = 15~17v,
t = 20~30分钟, δ= 10~15μm, T = 25~30℃。
二、 加入添加剂
加入添加剂NiSO,使电解液导热性↑.
工艺条件:NiSO10g/l, I = 2A/dm, t = 25分钟。
三、 混合法①+②
第四节 其它阳极氧化工艺
一、 硬质阳极氧化
生成硬度高、耐磨性好的厚氧化膜。
纯Al上的氧化膜硬度H= 1200~1500kgf/mm
(超过了淬火工具钢和铬镀层的硬度)
Al合金上的氧化膜硬度H= 250~500kgf/mm
膜层最大厚度可达250~300μm
工艺条件:
二、 瓷质阳极氧化(膜灰白色)
配方及工艺条件:(略)
三、 硫酸交流电阳极氧化
交流电阳极氧化膜层薄(<10μm)、发黄、硬度↓,工业上几乎不采用。可加入草酸、甘油及添加剂。
第四章 铝及铝合金电解着色
根据其显色色素体所在的位置不同,着色方法有:化学染色法、自然发色法、电解着色法、有机涂层着色法和复合着色法。
第一节 化学染色法
化学染色法是最早用于铝阳极氧化膜着色的方法。
一、 特点:工艺简单,作业性好,效率高,成本低,色域宽,色泽鲜艳。
二、 方法:
分两大类
一液法
无机染料染色法
二液法
化学着色 酸性有机染料
水溶性染料
有机染料染色法 碱性有机染料
油性染料
三、 化学染色的机理
化学染色是色素体靠氧化膜多孔层的物理和化学作用吸附于表面层内侧。铝阳极化膜具有30%的孔隙率,有巨大的比表面积和化学活性。
靠染料分子或离子的静电力进行的吸附叫物理吸附,吸附力取决于氧化膜的表面电位和染料性质。
所谓化学吸附指氧化膜与色素体以化学键、共价键或形成络合物等形式结合。
与化学吸附相比,物理吸附较弱,且受染色液温度的影响较大,所以化学着色的色牢度取决于化学吸附作用。
四、 无机染料染色
1、 一液法:将阳极氧化膜浸入一种溶液中,这种金属盐在膜孔
内水化生成色淀而使膜层显色。
2、 二液法:将阳极氧化膜先浸入一种盐溶液中,取出经清洗后
再浸入另一种盐溶液中,两次浸渍吸附的盐发生反应生成不可溶的沉淀色素,使制品显色。
五、 有机染料染色
用于铝阳极氧化膜染色的水溶性酸性染料主要有蒽醌系偶氮基以及三苯甲烷类。
六、 工艺流程
基本上是:
预处理(同常规)→ 硫酸阳极氧化→ 水和纯水洗→ 染色→ 水和纯水洗→ 沸水封孔→ 烘干
第二节 自然发色法
自然发色法指铝材在有机酸水溶液中经阳极氧化的同时而着色的方法。由于氧化和着色一步完成,所以也叫一步法。
自然发色法(又称电解整体着色法)按着色原因不同,又可分为:
合金发色法(次地位)、电解发色法(占主导)、电源发色法(开发中)
一、 着色原理:
众说不一,原理不十分清楚,有如下观点:
1、 合金元素及基体金属一起阳极氧化后残留于氧化膜中。
2、 氧化膜中积累了由有机酸还原成的碳。
3、 氧化膜中积累了有机酸生成的焦油状物质。等等
二、 合金发色法
由于合金元素不同,阳极氧化时这些元素不溶于电解液而残留在氧化膜结构中,其色素体是合金元素。
三、 电解发色法
采用有机酸作主要成份,加入少量硫酸,在高电压大电流密度下着色,(DC电流)。
此法主要用在建筑型材的氧化着色上。因其氧化膜在耐蚀性、耐候性、耐磨性方面都优于电解着色和化学染色法,曾广泛用于铝门窗、阳台、围栏等建筑型材及车辆外装材上。
但在使用过程中发现成本高(耗电量为浅田法的5 ~ 6倍),色种少(色调受合金限制),控制要求严,所以逐渐被电解着色法所代替。
四、 电源发色法
采用普通硫酸氧化液,施加换向电流、不对称电流或脉冲电流,由于电源波形变化,使硫酸中的硫被还原,残留于氧化膜中而显色。
第三节 电解着色
一、电解着色的概念及发展历史
将阳极氧化后的铝材浸在金属盐的水溶液中进行交流电解,使金属盐沉积在氧化膜孔中而着色的方法,称为电解着色法。
日本人将电解着色法叫浅田法,国际上通称电解着色法或二次电解着色法。
二、电解着色的发展趋势
1、防护—装饰性着色膜的发展趋势
2、电解着色在机能方面的发展趋势
三、电解着色膜的特点和着色液的分类
1、电解着色膜的特点
2、电解着色液的分类(见后面附录)
四、电解着色的原理
电解着色实质是电镀,即是金属离子的一种电化学还原现象。将阳极氧化铝置于金属盐溶液中,施加低压交流电,金属离子被电化学还原,以胶粒子状态沉积在氧化膜孔隙的底部,通过金属胶粒对光的散射作用而显色的一种方法。
1、氧化膜的结构和性质
阻挡层——厚150Å
硫酸阳极化膜→ 孔径约120 Å
10um厚复合膜 多孔层 孔壁厚约300 Å
孔密度4 ~ 5亿孔/mm
2、浅田法铝阳极氧化电解着色的必要条件:
1)、采用酸性水溶液、交流电;
2)、使用低电流密度0.1~0.35A/dm;
3)、采用的重金属盐能溶于水,且具还原和氧化作用;
4)、采用惰性材料,如石墨、不锈钢作对电极。
五、电解着色液
铝建筑型材着色膜以青铜系应用最为普及,九十年代约占我国铝电解着色的95%以上。青铜色系包括香槟色(浅青铜色)——青铜色——深青铜色(棕色)——咖啡色——古铜色——黑色等六色,其中咖啡色只有在Ni—Sn混盐中才能获得。有许多单金属盐(Ni、Co、Sn)着色液和混盐着色液(Ni—Sn、Ni—Co、Ni—Zn、Ni—Mn、Pb—Zn)等都可以获得青铜色系。我国工业上应用的有Ni、Co、Sn和Ni—Sn混合盐。应用最多的是Sn盐和Ni—Sn混合盐,其次是Ni盐。
1、Sn盐电解着色
使用这种方法可以得到浅黄——青铜——黑色色系。
㈠工艺特点:
①色调范围广,可获得从香槟至黑色的全部色系(咖啡色除外);
②着色分散能力和重现性好,色差小,色调均匀稳定,适合于各种复杂型材;
③着色膜的耐光性、耐蚀性、耐候性优良,在欧洲大型建筑上使用近30年,色泽依旧;
④成份简单,操作方便,易于控制;
⑤对杂质的容忍度高;
⑥着色速度快,生产效率高,通常着色一次约4 ~ 5分
钟(古铜色),故一个着色槽可承担3 ~ 4个氧化槽的生产任务;
7 成本较低,可使用普通的50H工频电源;
8 二价锡Sn稳定性差,容易氧化水解变质。
㈡主要成份及其作用:
Sn盐电解着色的典型配方:SnSO10~g/l,HSO15~30g/l,
有机酸 15~30g/l
由于无论是Sn还是Sn都有较大的水解倾向,当酸度较低时,最易发生下列水解反应:
SnSO+2HO→Sn(OH)↓+HSO
Sn(SO)+4HO→Sn(OH)↓+2HSO
→HSnO↓+HO
时间不长,溶液就会浑浊得不可使用。因此,需加入作为稳定剂的有机酸。
⒈SnSO亚锡盐为着色主盐,靠Sn在膜孔中电沉积而显色。
⒉HSO提高电导率,防止亚锡盐氧化水解及提高着色均匀性。
⒊添加剂(着色添加剂)
① 抗氧化剂(稳定剂):抑制Sn氧化成Sn,缓冲剂HBO使Sn→Sn速度↓↓
2 还原剂:可防止Sn→Sn,又可使部分Sn→Sn;
3 提高分散率(减小色差):HS、酚磺酸、氨磺酸、苯磺酸
4 提高导电率:酒石酸、柠檬酸、酒石酸铵
5 防止白斑:MgSO
㈢着色液配方及工艺条件(略):
㈣各种影响电解着色的因素:
⒈合金成份:合金成份对电解着色膜影响的实质是合金元素与铝形成固溶体的程度和析出状态,严重影响铝阳极化膜的表面和内在质量。
凡能形成均匀连续的阳极化膜,膜层本身不带深颜色,而阻挡层有整流的作用的铝合金均能进行电解着色。
2 SnSO含量:SnSO含量越高,着色速度越快,颜色越深。含量过
高时,析出过快,逸出孔外产生锡灰。SnSO含量太低,着色很慢,难以得到深青铜色。生产上,生产浅古铜和中古铜时用8 ~ 15g/l;生产深古铜和黑色时用15 ~ 20g/l
3 HSO含量:HSO含量↑导电性↑,防止Sn→Sn及水解,但
着色速度↓(∵H有碍于Sn沉积)。HSO含量↓导电性↓,Sn易→Sn及水解,着色速度↓。含量由低→高,色调由红→黄。一般控制在15 ~20为宜,PH=0.8~1.6
4 工作电压:随V↑着色速度↑→Vmax→V↑↑→着色速度↓且氧
化膜剥落,产生白点。着色电压一般选在15 ~ 18v。
为在一定时间內着出规定的色调,常采用定电压下进行着色,在恒电压下,电流—时间的关系是一条衰减曲线。
5 槽液温度:T↑,Sn扩散速度↑,导电性好,着色速度↑,颜色加↑,但易Sn→Sn及水解加快。要求控制20±2℃。
6 着色时间:当着色电压一定,t↑,色调由浅→深。根据电压、温度、槽液浓度确定t。
7 PH值:PH↑易Sn→Sn(PH=1.5±0.5)。PH值不当 :① 颜色不正;② 着色不均匀
8 氧化膜厚:着深古铜δ>5μm即可;着黑色 δ>12μm以上
9 极比及其分布和间距:极比——即电极的表面积和铝型材表面积之比。着色是定电压作业,极比太小会降低铝材上的电流密度,导致:① 在膜中沉积析出量,着不出深色;② 着色不均匀(过大过小均会)。极间距——太小→磁场干扰→着色不均;太大→着色t↑。一般情况下,着色电流I = 0.2~0.3A/dm时极比应是1:1。
生产实践证明,最佳极比是1:0.75~0.8之间;阴阳极间距为250~300mm。
10 杂质:Sn盐电解着色液抗杂质性能过胜过其它盐类,危害最大的
杂质是K、Na、NO、Cl。
㈤空气及杂质对槽液稳定性的影响:⒈空气搅拌。⒉Fe、Cu
㈥着色液的老化问题:①有害杂质的污染②Al的积累③Me的氧化④添加剂的分解。
2、Ni盐电解着色
(一)工艺特点⑴单Ni盐着色可获得香槟色、青铜色、深青铜、古铜至黑色,获深黑较困难;⑵成份简单,十分稳定;⑶原料来源广,成本低;⑷着色膜耐光性、耐磨性、耐候性与Sn盐相当;⑸着色液分散能力差,大面积型材着色不均匀;⑹对杂质比较敏感,尤其对Na、K。由于最后二个的原因,Ni盐槽被Sn盐所取代。
(二)主要成份
硫酸镍、硼酸、酒石酸、硫酸铵、硫酸镁等。
(三)典型工艺
浅田法主要工序:
硫酸阳极氧化(膜厚δ=7~9μm)
Ni盐电解交流着色(青铜色)
电泳涂漆或浸渍涂漆法(丙稀酸透明漆δ=7~9μm)
Ni盐电解着色工艺:
NiSO·7HO 25g/l,MgSO·7HO 20g/l,(NH)SO15g/l,,HBO25g/l
PH=4.4,V=7~15v,I=0.1~0.8A/dm,50Hz,T=15~25℃,t=2~15’
3、Ni—Sn混合盐电解着色
为解决纯Ni盐电解着色的缺点,人们研究了Ni—Sn混合盐电解着色法,其优点:①着色速度快;②可得到单一Ni盐得不到的纯黑色;③由于Sn盐含量低,只占Sn盐法的1/4左右,所以溶液稳定性好,成本低。
(一)Ni—Sn盐着色机理
Ni盐在溶液中不参与电化学反应,只起催化剂作用。
(二)工艺规范
NiSO30g/l, HBO30g/l,SnSO5g/l, HSO18g/l
稳定剂 10g/l,温度 20~30℃,AC 14~16 v,时间 2~10 min
电极:不锈钢或石墨
(三)各成份的作用
第三节 有机涂层着色
浸渍涂漆法
静电粉末喷涂
静电喷涂法
静电喷漆
电泳涂漆法
第五章 封孔处理
封孔处理是为改善阳极化铝的耐蚀性和物理性能为目的而进行后处理的总称。
封孔目的:提高氧化膜的防污染、抗腐蚀、耐磨等性能,还可提高表面性能和美观。
封孔处理方法:
常压水蒸汽
水合封孔—— 加压水蒸汽
沸水
化学法 无机质封孔——常温(或中温)封孔
有机质封孔 涂布或浸渍合成树脂
涂布或浸渍油脂
无机质封孔 在胶体溶液中进行电化学处理
电化学法 在无机盐中进行电化学处理
有机质封孔——电泳合成树脂漆、静电喷粉
第一节 水合封孔
一、机理
高温封孔的本质是铝氧化膜的水化反应,即将具有很高化学活性的非晶质氧化膜变成化学钝态的结晶质氧化膜的过程。
化学反应通式:
AlOAlO·nHO
该反应在常温和高温下都能进行,水化反应结合水分子的数目为1 ~ 3个,依温度而变。
T<80℃时,
γ-AlO-→2AlOOH+2HO→γ-AlO·3HO
(三水铝石)
这种水化氧化膜稳定性差,具有可逆性,水温愈低,可逆性愈大。
T>80℃时,
γ-AlO-→2AlOOH+HO→γ-AlO·HO
(勃母石or一水铝石)
这种水化氧化铝是稳定而不可逆的。
由于此反应使氧化膜体积膨胀38%,从而使氧化膜表面微孔封闭。
二、工艺
1、纯水封孔
纯水(去离子水),T=85~95℃,t=20~30’,PH=6±0.5
∵封孔时间↑,容易起粉霜(又称封闭华),封孔质量也不在好
∴目前基本淘汰
水合封孔的缺点:
1 能耗大,劳动条件差, T =85~95℃;
2 易产生“粉霜”,颜色↓;
3 时间长20分。
第二节 常温封孔
(冷封孔)
一、发展史
二、封孔原理
一般认为是以下三种作用的综合结果:
1) 水化作用
同样利用其水化作用生成亚稳态的γ-AlO·3HO,由于低温,水化反应速度慢,水化产物具有可逆性。
2) 金属盐的水解作用
是常温封闭的主反应,采用Ni-Co-F体系时,金属离子渗入膜孔中,在一定的PH值下发生水解,Ni、Co生成氢氧化物Ni(OH)与水化作用生成的水化氧化铝一起沉积,堵塞了孔隙。
3) 形成铝的化学转化膜
利用封孔剂中某些组分物质与铝材氧化膜的化学作用,在铝膜表面生成稳定的化学转化膜。
三、封孔工艺
添加剂:按要求。PH值缓冲剂:0.5~1g/l。极性溶剂:微量。
PH值:5.5~6.5(用醋酸or氨水调节)。温度:18~40℃。
时间(min):1μm/min。
主要成份控制:Ni/Co0.8~1.5g/l,F300~1400ppm
四、各成份的作用:
1) Ni盐:属于最主要成份,由于它在膜孔中的水解而实现封孔。
2) 氟化物:F在封孔过程中起媒介或催化剂作用。
3) 极性溶剂:①可能与Ni生成一种复杂的络合物,对封孔起到良好的影响。②促进表面活性剂溶液对氧化膜的湿润作用,增加Ni盐对膜孔的渗透能力。
五、影响封孔质量的主要因素:
1) PH值:PH值↑ Ni吸收量↑ PH=6.5达最大,一般控制在5.5~6.5之间。PH>6.5,Ni大量水解,产生白灰。
2) 温度T:T在25℃时吸收Ni最多,T↑吸收量↓。一般控制在20~30℃之间。
3) 陈化时间t:陈化时间t↑,封孔质量↑;一般规定24h后再做失重检查。
六、常见故障
1) 封孔不合格。原因:① 槽液组份含量不匹配;② 水质不合格;
③ PH值↓(水洗不净,带入残H); ④ 封孔时间不够; ⑤ 有害杂质长期积累太多。
2) 起白灰。原因:① F含量或组份中某成份含量高,加速封孔过
程(缩短封孔时间)。 ② F含量偏低(添加成份)。
铝及其合金表面处理的分类:
方向性条纹——采用拉丝模压造成有方向性条痕
机械法 无方向性表面——采用喷砂等造成点状凸凹痕
光亮表面——采用机械磨光、抛光
MBV法
化学氧化 EW法 —化学着色—封闭或涂化
LW法
化学法 化学抛光
化学镀镍等
化学刻蚀——无光化处理或化学砂面
电抛光 化学浸渍着色法
硫酸法 电解整体着色法
电化学法 阳极化—— 电解着色法
草酸法、铬酸法、磷酸法、混酸法
电镀——锌、黄铜、铜—镍—铬、硬铬、锡
蒸汽法
高温法 加压蒸汽法
沸水法
阳极化 中温法
膜后处理 常温法 电泳涂漆
有机质屏蔽 粉末喷涂
电解着色液的分类:
依其电解液组成、性质不同和工艺方法不同,可分为下列类型:
强酸性溶液:Sn、Cu、Ag盐等
单盐溶液 中性溶液:Ni、Co、Fe盐等
碱性溶液:Ni、Sn、Cu盐等
含氧酸盐溶液:钼酸盐、钨酸盐、硒酸盐、
高锰酸盐等
多金属盐溶液:Ni—Sn、Ni—Cu、Cu—Sn、Ni—Co、Ni—Zn等
两种溶液连续着色:Cu → 高锰酸盐、Cu → Ni盐
Cu → Ag盐、Ag → Cu盐等
三槽三段着色:多色着色、干涉光着色

我们欢迎各方(自)媒体、机构转载、引用我们原创内容,但需严格注明来源。同时,我们也倡导尊重与保护知识产权,如发现文章内容涉及侵权,请通过在线咨询进行投诉,我们会在第一时间核实处理。