铝合金喷涂前表面处理工艺配方以及特点分析
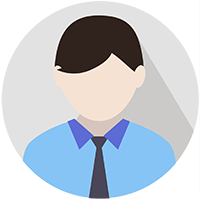
盟友2568974510
2023-05-29 08:25

+1
取消

+1
取消

微信扫一扫分享给朋友
铝合金表面处理的酸蚀脱脂工艺将传统工艺的脱脂、碱蚀、除污出光三道工序合为一道工序,降低成本和节省能源,经处理后的铝合金表面平滑光洁,保持铝合金原有的光泽,铝材溶解损耗量和槽液沉淀少,与铬酸盐转化处理配套性能好,特别适用于铝合金型材喷涂前的表面处理。
喷涂铝合金型材具有优良的耐蚀性和耐候性,坚固耐用,外观装饰好,生产工艺比阳极氧化简单,环保安全等特点,在建筑、装潢、运输等行业得到广泛应用。
铝合金型材在喷涂前处理中必须进行化学清洗和浸蚀,清除其表面粘附的油脂、自然氧化膜和灰尘等污染物,使铝合金基体裸露出来,形成均匀的活化表面,这是保证铬酸盐转化膜质量和喷涂质量的关键。
一、铝合金型材喷涂前处理工艺
工艺流程:工件装挂→酸蚀脱脂→水洗→水洗→铬酸盐转化处理→水洗→纯水洗→沥水→烘干→喷涂→固化。
铝型材喷涂前处理生产线分为全自动喷淋立式线和间歇式全浸渍卧式线两种。立式线适用于批量大、形状简单的工件,生产效率高,处理质量稳定,缺点是设备复杂、投资大;卧式线适宜处理形状复杂的工件,投资少,应用广,缺点是处理速度较慢、生产效率低。
酸蚀脱脂工艺配方和参数:硫酸(97%),30g/L-50 g/L;氟化氢铵,3 g/L-8 g/L;柠檬酸,2 g/L-4 g/L;硝酸钠,1 g/L-3 g/L;硫酸铁,0.5 g/L-1.5 g/L;二丙二醇,1 g/L-2 g/L;脱脂剂,0.1 g/L-0.5 g/L;温度,5℃-40℃;时间,3min-5min浸渍,1min-3min喷淋;喷淋压力,0.1MPa-0.2MPa.
二、酸蚀脱脂工艺配方成分和工艺参数的影响
1.硫酸
稀硫酸是一种非氧化性的无机酸,对铝合金型材有轻微的化学浸蚀作用,使用成本较低,酸雾挥发性少。硫酸能溶解、剥离铝及铝合金表面形成的自然氧化膜;裸露的铝合金基体与硫酸发生反应,起到活化铝表面的作用。当槽液中硫酸浓度低于30%时,铝的化学溶解速度随硫酸浓度的增加而缓慢地增加,铝材溶解损耗量少;当槽液中硫酸浓度超过30%以后,铝的腐蚀速度迅速加快,易产生过腐蚀,光亮度下降。一般来说,槽液中硫酸浓度不宜超过15%。
2.氟化氢铵
氟离子在酸蚀脱脂液中作脱除氧化膜的加速剂,能加速溶解铝表面的氧化膜,消除或减少挤压模痕和其他缺陷,使铝型材表面平整光洁、均匀一致。氟是一种体积小、电负性较强的卤族元素,对铝能起强烈的氧化作用,与杂质有一定的络合能力,能溶解铝合金表面的锰、铜、硅等合金元素和杂质,抑制和除去铝材上的黑色挂灰,获得较光亮的金属表面。氟化氢铵的化学稳定性强于氢氟酸的,对人体皮肤的伤害作用小于氢氟酸的,因此,采用氟化氢铵取代氢氟酸为溶液提供氟离子,在生产中使用比较安全,还可以减轻氟离子对不锈钢设备的腐蚀。脱除氧化膜的腐蚀速度随氟化氢铵浓度的增加而增长,氟化氢铵含量不宜过高,否则反应剧烈易造成过腐蚀,降低铝表面光泽,不利于后续的铬酸盐转化处理。
3.柠檬酸
柠檬酸在酸蚀脱脂液中主要起缓蚀作用,能有效地抑制铝在酸性介质中的腐蚀。柠檬酸是三元有机酸,能在铝基体表面进行物理和化学吸附,改变金属/溶液界面的双电层结构,增加金属离子化过程的活化能,从而使腐蚀速度减慢,降低铝材的损耗量,避免发生过腐蚀。柠檬酸是金属离子的络合剂,能与从酸蚀液中溶解下来的铝、镁、铁等离子形成稳定的络合物,减少槽液中铝离子的含量,掩蔽槽液中杂质的干扰,使溶液稳定,减少沉淀,从而延长酸蚀脱脂液的使用寿命。柠檬酸的加入,对减少铝损耗、降低化工材料消耗、减少槽液沉渣、改善操作条件均有一定的作用。
4.硝酸钠
硝酸钠是酸蚀脱脂液中的氧化剂,对铝合金具有良好的光亮和整平效果。硝酸钠的作用是使铝材表面发生氧化反应,形成的氧化铝钝化膜遏制了铝表面凹陷处的酸性择优浸蚀,使铝型材的腐蚀面平整、光洁。
5.硫酸铁
三价铁离子能加速对铝型材表面进行腐蚀和脱除氧化膜,Fe3+可以在铝材表面发生置换反应,形成微电池,使铝表面产生微量氢气,将油污带出铝表面,反应过程AL+ Fe3++2H+→AL3++Fe2++H2↑。槽液中的氧化剂能将上述反应产生的Fe2+重新氧化成Fe3+,减少Fe2+的积累,使槽液稳定,因此Fe3+在反应过程中自身不消耗,主要起促进作用,可提高铝材的除污速度和光洁度。
6.二丙二醇
在酸蚀脱脂液中加入二丙二醇等易溶于水、微毒类的有机低分子增溶剂,能大大降低溶液的表面张力,显著改善酸蚀脱脂液的清洗能力和溶液稳定性。油脂的分子结构中有较长的烃基,与有机溶剂的结构相似,可以互相溶解,因此,利用有机溶剂对油脂具有很强的溶解能力的特点,可以提高酸蚀脱脂液的脱脂效果。
7.脱脂剂
铝材表面上的油脂通常可分为矿物油脂和动植物油脂两大类型,表面活性剂对上述油脂有良好的润湿、乳化能力,在酸蚀脱脂过程中,表面活性剂吸附在油与溶液的界面上,其亲水基因指向溶液,亲油基因指向油污,定向地排列,使油和溶液的界面张力大大降低,油脂在金属表面的附着力减弱,在酸腐蚀金属产生氢气的机械剥离作用下,油污松动,容易分散成极小的油珠脱离金属表面悬浮于溶液中,表面活性剂的增溶作用可防止脱下来的油污再粘附到铝材表面。常温下提高除油效率的关键是表面活性剂的选择和配比优化,应根据表面活性剂的表面张力、浊点、临界胶束浓度以及亲憎平衡值(HLB值),选择多种对油污吸附性、润湿性和分散性好,渗透力和乳化力特别强,泡沫少,生物降解性好,在酸性溶液中性能稳定的阴离子型和非离子型表面活性剂进行复配,复配时要将HLB值调整至12-16,以适合溶液清洗的范围。复配后两者的协同效应可以达到互相补偿及增效之目的,使溶液的表面张力和临界胶束浓度下降,浊点升高,表面活性增加,润湿性能和净洗作用都得到明显的改善。在采用喷淋方式进行酸蚀脱脂时,由于机械力的作用会产生大量泡沫,使溶液以泡沫的形式大量从槽中溢出,因此,应加入适量的消泡剂抑制泡沫的产生。试验表明,选择磺酸盐类阴离子型表面活性剂和烷基酚聚氧乙烯醚、聚醚类非离子型表面活性剂进行复配,可以获得良好的除油效果。
8.温度
试验结果表明,除油脱除氧化膜的速度随温度升高而加快,温度的升高可以降低油污黏度和界面张力,提高酸液对铝材的浸蚀能力,增强表面活性剂与油污的乳化作用。温度低于5℃时,除油脱除氧化膜的速度减慢,影响生产进度;温度高于40℃时,酸蚀脱脂液组分易挥发,产生酸雾,酸液损耗增大,能耗增加,铝材易产生过腐蚀和黑色挂灰。因此,酸蚀脱脂液的使用温度应控制在5℃-40℃范围内。
9.时间
处理时间过短,工件表面的油污、自然氧化膜没有完全除净,会阻碍铬酸盐转化成膜反应的正常进行;处理时间过长,会使铝的损耗量增加,工件表面粗糙,光泽度下降,生产效率降低。处理时间与铝材成分、表面油污的多少、自然氧化膜的厚度、处理温度和方式等密切相关,一般取1min-5min,以油污、自然氧化膜完全清除干净为原则来确定该工件的最佳酸蚀脱脂时间。
三、酸蚀脱脂工艺的应用
1.槽液配制
先在槽中加入1/2体积的自来水,在搅拌下缓慢加入计算量的浓硫酸,冷却至40℃左右;再依次加入计算量的氟化氢铵、柠檬酸等其他化学药品,搅拌至完全溶解;然后加水至规定体积,搅拌均匀,测定酸度后即可投入使用。
2.槽液管理
随着铝合金型材处理量的不断增加,酸蚀脱脂液在使用过程中不断被消耗、带出,酸度和脱脂效果降低,各种有效成分逐渐下降,因此,应定时定期分析槽液,及时补加硫酸、氟化氢铵和其他化学药品,使槽液各工艺参数保持在规定范围内。工件表面的油污被置换、分散、凝集后悬浮于酸蚀脱脂液表面,需经常把液面上的油污溢流掉,以防止工件出槽时二次沾上油污。长期使用后,当槽液中铝离子积累过高时,应部分或全部更换槽液。
3.质量检验
目视检查,经酸蚀脱脂液处理后铝合金型材表面露出金属本色,平整光亮,油污和自然氧化膜全部除净,水洗后水膜连续、完整,表面完全润湿,不挂水珠,无黑色挂灰和过腐蚀现象。
四、酸蚀脱脂工艺优越性分析
1.酸蚀脱脂工艺将脱脂、碱蚀、除污出光等工序一次性完成,与分槽处理工艺相比,简化工序,减少占地面积和设备投资,节约化工原料和清洗用水。
2.常温使用,槽液不需要加热,节省能源,无酸雾挥发,不污染工作环境,能抑制酸性物质对不锈钢设备和厂房的侵蚀,延长清洗设备和厂房的使用寿命。
3.清除油污能力强,脱除氧化膜速度快,缓蚀效率高,铝材溶解损耗量少,无过|来源腐蚀和黑色挂灰现象。工件处理后呈银白色,光洁发亮,表面质量好。
4.溶液性能稳定,沉淀物少,管理维护方便,槽液可连续循环使用期长,每槽可用1年以上。
喷涂铝合金型材具有优良的耐蚀性和耐候性,坚固耐用,外观装饰好,生产工艺比阳极氧化简单,环保安全等特点,在建筑、装潢、运输等行业得到广泛应用。
铝合金型材在喷涂前处理中必须进行化学清洗和浸蚀,清除其表面粘附的油脂、自然氧化膜和灰尘等污染物,使铝合金基体裸露出来,形成均匀的活化表面,这是保证铬酸盐转化膜质量和喷涂质量的关键。
一、铝合金型材喷涂前处理工艺
工艺流程:工件装挂→酸蚀脱脂→水洗→水洗→铬酸盐转化处理→水洗→纯水洗→沥水→烘干→喷涂→固化。
铝型材喷涂前处理生产线分为全自动喷淋立式线和间歇式全浸渍卧式线两种。立式线适用于批量大、形状简单的工件,生产效率高,处理质量稳定,缺点是设备复杂、投资大;卧式线适宜处理形状复杂的工件,投资少,应用广,缺点是处理速度较慢、生产效率低。
酸蚀脱脂工艺配方和参数:硫酸(97%),30g/L-50 g/L;氟化氢铵,3 g/L-8 g/L;柠檬酸,2 g/L-4 g/L;硝酸钠,1 g/L-3 g/L;硫酸铁,0.5 g/L-1.5 g/L;二丙二醇,1 g/L-2 g/L;脱脂剂,0.1 g/L-0.5 g/L;温度,5℃-40℃;时间,3min-5min浸渍,1min-3min喷淋;喷淋压力,0.1MPa-0.2MPa.
二、酸蚀脱脂工艺配方成分和工艺参数的影响
1.硫酸
稀硫酸是一种非氧化性的无机酸,对铝合金型材有轻微的化学浸蚀作用,使用成本较低,酸雾挥发性少。硫酸能溶解、剥离铝及铝合金表面形成的自然氧化膜;裸露的铝合金基体与硫酸发生反应,起到活化铝表面的作用。当槽液中硫酸浓度低于30%时,铝的化学溶解速度随硫酸浓度的增加而缓慢地增加,铝材溶解损耗量少;当槽液中硫酸浓度超过30%以后,铝的腐蚀速度迅速加快,易产生过腐蚀,光亮度下降。一般来说,槽液中硫酸浓度不宜超过15%。
2.氟化氢铵
氟离子在酸蚀脱脂液中作脱除氧化膜的加速剂,能加速溶解铝表面的氧化膜,消除或减少挤压模痕和其他缺陷,使铝型材表面平整光洁、均匀一致。氟是一种体积小、电负性较强的卤族元素,对铝能起强烈的氧化作用,与杂质有一定的络合能力,能溶解铝合金表面的锰、铜、硅等合金元素和杂质,抑制和除去铝材上的黑色挂灰,获得较光亮的金属表面。氟化氢铵的化学稳定性强于氢氟酸的,对人体皮肤的伤害作用小于氢氟酸的,因此,采用氟化氢铵取代氢氟酸为溶液提供氟离子,在生产中使用比较安全,还可以减轻氟离子对不锈钢设备的腐蚀。脱除氧化膜的腐蚀速度随氟化氢铵浓度的增加而增长,氟化氢铵含量不宜过高,否则反应剧烈易造成过腐蚀,降低铝表面光泽,不利于后续的铬酸盐转化处理。
3.柠檬酸
柠檬酸在酸蚀脱脂液中主要起缓蚀作用,能有效地抑制铝在酸性介质中的腐蚀。柠檬酸是三元有机酸,能在铝基体表面进行物理和化学吸附,改变金属/溶液界面的双电层结构,增加金属离子化过程的活化能,从而使腐蚀速度减慢,降低铝材的损耗量,避免发生过腐蚀。柠檬酸是金属离子的络合剂,能与从酸蚀液中溶解下来的铝、镁、铁等离子形成稳定的络合物,减少槽液中铝离子的含量,掩蔽槽液中杂质的干扰,使溶液稳定,减少沉淀,从而延长酸蚀脱脂液的使用寿命。柠檬酸的加入,对减少铝损耗、降低化工材料消耗、减少槽液沉渣、改善操作条件均有一定的作用。
4.硝酸钠
硝酸钠是酸蚀脱脂液中的氧化剂,对铝合金具有良好的光亮和整平效果。硝酸钠的作用是使铝材表面发生氧化反应,形成的氧化铝钝化膜遏制了铝表面凹陷处的酸性择优浸蚀,使铝型材的腐蚀面平整、光洁。
5.硫酸铁
三价铁离子能加速对铝型材表面进行腐蚀和脱除氧化膜,Fe3+可以在铝材表面发生置换反应,形成微电池,使铝表面产生微量氢气,将油污带出铝表面,反应过程AL+ Fe3++2H+→AL3++Fe2++H2↑。槽液中的氧化剂能将上述反应产生的Fe2+重新氧化成Fe3+,减少Fe2+的积累,使槽液稳定,因此Fe3+在反应过程中自身不消耗,主要起促进作用,可提高铝材的除污速度和光洁度。
6.二丙二醇
在酸蚀脱脂液中加入二丙二醇等易溶于水、微毒类的有机低分子增溶剂,能大大降低溶液的表面张力,显著改善酸蚀脱脂液的清洗能力和溶液稳定性。油脂的分子结构中有较长的烃基,与有机溶剂的结构相似,可以互相溶解,因此,利用有机溶剂对油脂具有很强的溶解能力的特点,可以提高酸蚀脱脂液的脱脂效果。
7.脱脂剂
铝材表面上的油脂通常可分为矿物油脂和动植物油脂两大类型,表面活性剂对上述油脂有良好的润湿、乳化能力,在酸蚀脱脂过程中,表面活性剂吸附在油与溶液的界面上,其亲水基因指向溶液,亲油基因指向油污,定向地排列,使油和溶液的界面张力大大降低,油脂在金属表面的附着力减弱,在酸腐蚀金属产生氢气的机械剥离作用下,油污松动,容易分散成极小的油珠脱离金属表面悬浮于溶液中,表面活性剂的增溶作用可防止脱下来的油污再粘附到铝材表面。常温下提高除油效率的关键是表面活性剂的选择和配比优化,应根据表面活性剂的表面张力、浊点、临界胶束浓度以及亲憎平衡值(HLB值),选择多种对油污吸附性、润湿性和分散性好,渗透力和乳化力特别强,泡沫少,生物降解性好,在酸性溶液中性能稳定的阴离子型和非离子型表面活性剂进行复配,复配时要将HLB值调整至12-16,以适合溶液清洗的范围。复配后两者的协同效应可以达到互相补偿及增效之目的,使溶液的表面张力和临界胶束浓度下降,浊点升高,表面活性增加,润湿性能和净洗作用都得到明显的改善。在采用喷淋方式进行酸蚀脱脂时,由于机械力的作用会产生大量泡沫,使溶液以泡沫的形式大量从槽中溢出,因此,应加入适量的消泡剂抑制泡沫的产生。试验表明,选择磺酸盐类阴离子型表面活性剂和烷基酚聚氧乙烯醚、聚醚类非离子型表面活性剂进行复配,可以获得良好的除油效果。
8.温度
试验结果表明,除油脱除氧化膜的速度随温度升高而加快,温度的升高可以降低油污黏度和界面张力,提高酸液对铝材的浸蚀能力,增强表面活性剂与油污的乳化作用。温度低于5℃时,除油脱除氧化膜的速度减慢,影响生产进度;温度高于40℃时,酸蚀脱脂液组分易挥发,产生酸雾,酸液损耗增大,能耗增加,铝材易产生过腐蚀和黑色挂灰。因此,酸蚀脱脂液的使用温度应控制在5℃-40℃范围内。
9.时间
处理时间过短,工件表面的油污、自然氧化膜没有完全除净,会阻碍铬酸盐转化成膜反应的正常进行;处理时间过长,会使铝的损耗量增加,工件表面粗糙,光泽度下降,生产效率降低。处理时间与铝材成分、表面油污的多少、自然氧化膜的厚度、处理温度和方式等密切相关,一般取1min-5min,以油污、自然氧化膜完全清除干净为原则来确定该工件的最佳酸蚀脱脂时间。
三、酸蚀脱脂工艺的应用
1.槽液配制
先在槽中加入1/2体积的自来水,在搅拌下缓慢加入计算量的浓硫酸,冷却至40℃左右;再依次加入计算量的氟化氢铵、柠檬酸等其他化学药品,搅拌至完全溶解;然后加水至规定体积,搅拌均匀,测定酸度后即可投入使用。
2.槽液管理
随着铝合金型材处理量的不断增加,酸蚀脱脂液在使用过程中不断被消耗、带出,酸度和脱脂效果降低,各种有效成分逐渐下降,因此,应定时定期分析槽液,及时补加硫酸、氟化氢铵和其他化学药品,使槽液各工艺参数保持在规定范围内。工件表面的油污被置换、分散、凝集后悬浮于酸蚀脱脂液表面,需经常把液面上的油污溢流掉,以防止工件出槽时二次沾上油污。长期使用后,当槽液中铝离子积累过高时,应部分或全部更换槽液。
3.质量检验
目视检查,经酸蚀脱脂液处理后铝合金型材表面露出金属本色,平整光亮,油污和自然氧化膜全部除净,水洗后水膜连续、完整,表面完全润湿,不挂水珠,无黑色挂灰和过腐蚀现象。
四、酸蚀脱脂工艺优越性分析
1.酸蚀脱脂工艺将脱脂、碱蚀、除污出光等工序一次性完成,与分槽处理工艺相比,简化工序,减少占地面积和设备投资,节约化工原料和清洗用水。
2.常温使用,槽液不需要加热,节省能源,无酸雾挥发,不污染工作环境,能抑制酸性物质对不锈钢设备和厂房的侵蚀,延长清洗设备和厂房的使用寿命。
3.清除油污能力强,脱除氧化膜速度快,缓蚀效率高,铝材溶解损耗量少,无过|来源腐蚀和黑色挂灰现象。工件处理后呈银白色,光洁发亮,表面质量好。
4.溶液性能稳定,沉淀物少,管理维护方便,槽液可连续循环使用期长,每槽可用1年以上。
声明:说化有益·表面处理联盟网专业视角栏目旨在免费为同行提供知识共享和储存,所有文章均由业内专业人士发布(包括转帖),文末都会标注作者,版权归作者所有。文章仅代表作者本人的观点,本站不保证文章等内容的有效性。
知识互通,携手共进,我们欢迎各方(自)媒体,机构转载,引用我们原创内容,但需严格注明来源。同时,我们也倡导尊重与保护知识产权,如发现文章内容涉及侵权,请通过在线咨询进行投诉,我们会在第一时间核实处理。
相关视角